Quality Control
“Quality first” is our general principle. it also represents a company’s attitude towards responsibility. Thus, enkonn carries out its development and production in strict accordance with ISO9001 standards and procedures. Our QA laboratory adopts world-class equipment and facilities so as to get accurate data from inspection.
Detailed inspection items are below:
Raw material inspection
- Light source by Integrating Sphere
- Aging test of light source and controller
- Salt spray testing for aluminum components and coating parts
- Battery testing
Working and performance
- Working temperature testing by high and low-temperature equipment
- IP65 waterproof class test by simulating a raining environment
Packing and delivery
- Vibration testing
- Package structure
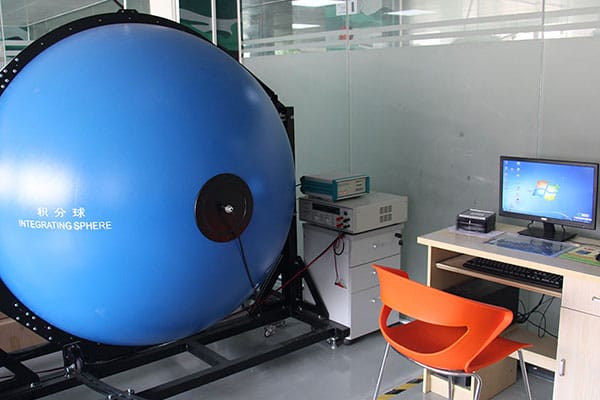
Integrating spheres for luminous flux
At a diameter of 1.9 meters, this equipment is designed for measuring light sources in an upright or suspended configuration, such as lumen, color temperature, power, color rendering index and so on. By using this equipment, our factory can choose the qualified LED light source according to the customers’ requirements.
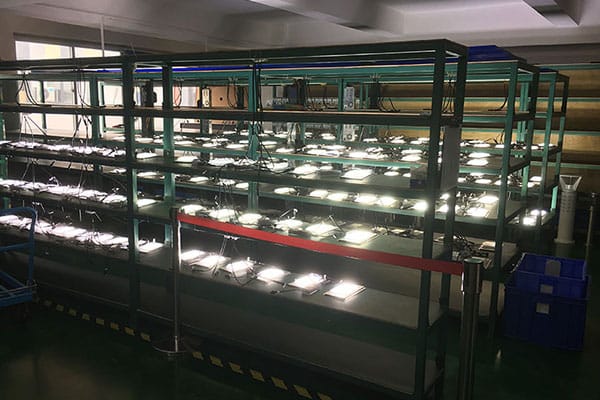
Aging Testing
Both lighting source and controller require aging testing before delivery. The aging process can eliminate components with a defect from being assembled with the product. We always test every unit, which takes 24-48 hours.
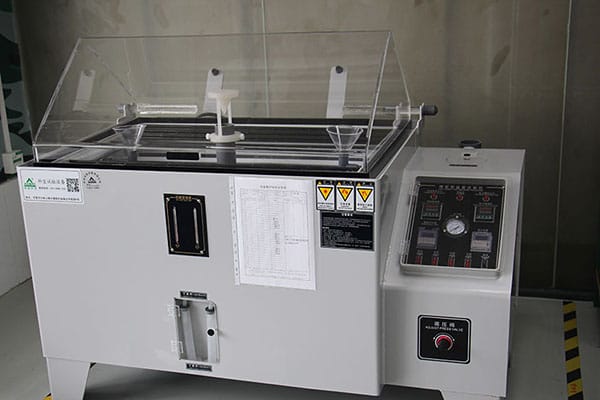
Salt Spray Testing
Salt spray testing is an accelerated corrosion test that produces a corrosive attack to coated samples in order to evaluate (mostly comparatively) the suitability of the coating for use as a protective finish.
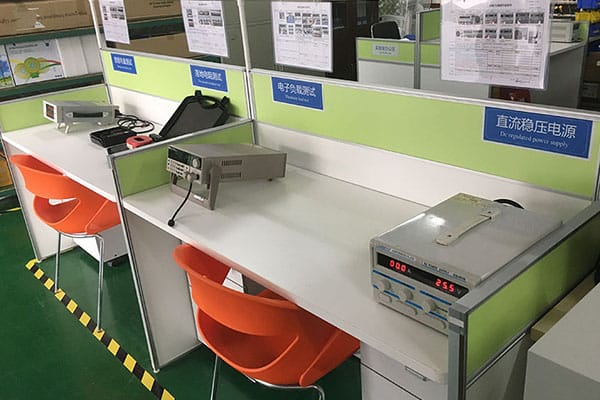
Battery Testing
Battery cycle testing is used to predict the lifespan of a battery by analyzing the data recorded by the special equipment.
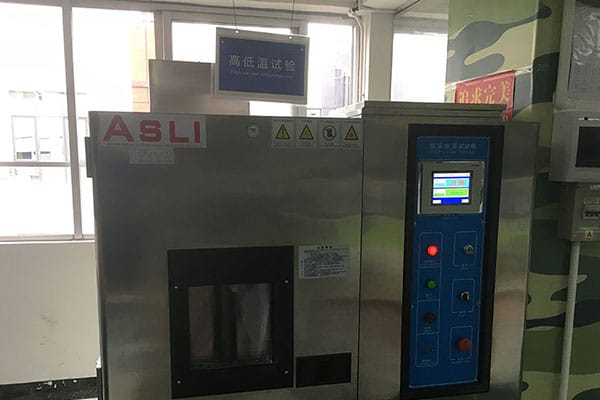
High or Low Surrounding Temperature Testing
By simulating streetlights’ extreme working environments, such as temperature and humidity, we can find out if its structure, as well as raw materials, is appropriate and qualified.
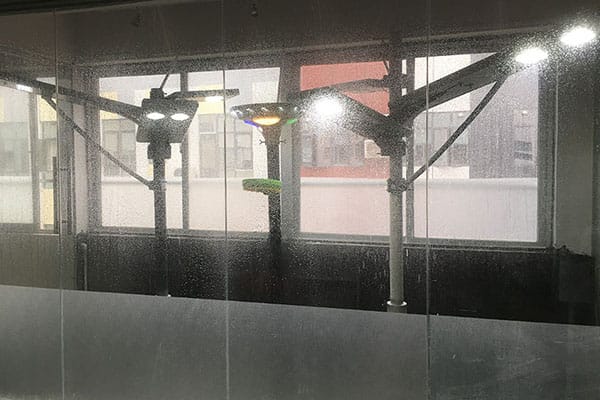
Waterproof and IP Rating Testing
Streetlights face some extreme working environments! This facility is well designed for mimicking such situations to check if it can meet IP65 class.
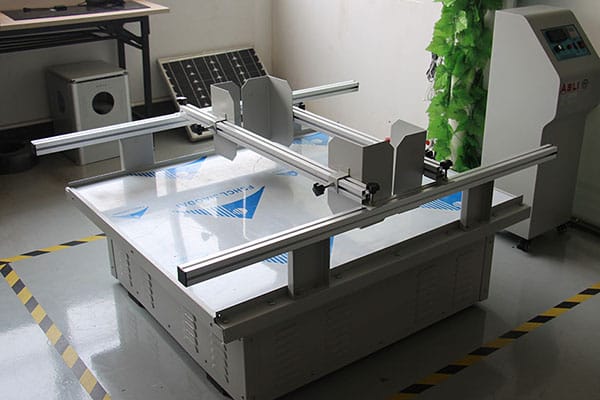
Vibration Testing
To check packing reliability, it is essential, during the packing design phase, that the machine simulates a vibration environment – just as if the packed product is being transported from a country to destination country.